It will soon be 10 years since we delivered the world’s first megawatt-class permanent magnet (PM) shaft generators. Using PM shaft generators instead of auxiliary gensets can significantly reduce fuel consumption. This also leads to lower emissions since less fuel needs to be burned.
Due to recently tightened emission regulations with the ultimate goal for the shipping industry to reach net-zero emissions by around 2050, shaft generator systems with PM technology have become a standard solution in large ocean-going vessels.
Until now, we have sold well over 300 in-line PM shaft generators for various vessel types, such as container vessels, LNG carriers, car carriers and various tankers. Now, we have several million cumulative operating hours with zero field failures, which proves the soundness of the technology.
While we expect the demand for PM shaft generator systems to continue at high levels for the foreseeable future, we have recently seen a rapid increase in another application as well: direct-drive electric propulsion.
Currently, the standard solution in large vessels, with the exception of cruise vessels, is to use a 2-stroke diesel engine to run the propeller. But this could start to change.
In diesel-electric propulsion, electric power is generated with diesel gensets and then fed via transformers and frequency converters to propulsion motors running the propellers. The obvious benefit is that there is no need for a large 2-stroke main engine, which has been used with conventional diesel-mechanical propulsion for a very long time.
Benefits of direct-drive electric propulsion
While the investment cost of a diesel-electric system is usually higher, since it requires more components in the whole power train – diesel engines, generators, transformers, frequency converters and electric motors – it has many benefits that make it an attractive solution for large vessels.
The total efficiency at a rated point is usually lower with diesel-electric systems than with diesel-mechanical systems. Still, vessels very rarely move at full speed to save fuel and lower emissions. This is because of the cubic dependence between propeller power and vessel speed. The power increases at the third exponent of speed.
You also can look at this the other way around. If you lower the vessel speed by 10%, your power demand will drop by almost 30%. The journey will take 10% more time, of course. Still, the benefits of an earlier arrival time at full speed cannot even closely outweigh the fuel savings and reduced emissions gained by reducing speed.
Lowering speed is a very effective way to cut down on a vessel’s CO2 emissions. PM machines in particular have the highest efficiency at partial load points. Furthermore, since there are always 4–8 gensets in large vessels, some of them can be switched off, while the remaining ones can operate at an optimal load point from a fuel consumption point of view.
Besides providing better overall efficiency, electric propulsion enables better passenger comfort, since electric machines run much more smoothly than slow-speed diesel engines. This is one of the main reasons all modern cruise vessels have been using diesel-electric propulsion for a long time.
In addition to lower operating expenses through better efficiency, maintenance costs for electric equipment are also generally lower than for big diesel engines. And especially with PM motors, there are very few wearing parts, further lowering maintenance costs.
Vessels with diesel-electric propulsion nearly always have two or three propulsion lines. This means that a single failure in any of the components in the power system will not result in more than a 50% loss of propulsion power, as 50% of the power can still move the vessel at 80% of its maximum speed.
A diesel-electric propulsion system also provides more freedom to the vessel designer since electric components can be located on a vessel much more flexibly than a big diesel engine. PM motors are also very compact due to high torque density, allowing more space for cargo and, therefore, resulting in a lower transportation cost per cargo unit.
And finally, if the vessel has batteries on board, it allows emission-free maneuvering in harbor areas, which is becoming more commonly required in many locations.
PM propulsion motor options
During the last couple of years, we have developed various propulsion concepts that are largely based on our existing product platform. Sometimes, it is beneficial for the propulsion shafts and bearings to be supplied by the system integrator, so our motor is identical to a shaft generator design, having no bearings or shaft. This makes the whole propulsion line simpler since common bearings can be utilized.
We already have such a system in operation on board the M/S Nukumi operating in the Great Lakes area in North America. For that vessel, we supplied variable-speed PM gensets, DC-Hubs and 3 MW direct-drive propulsion motors.
In several cases, our customers have requested a more conventional solution where the electric motor has its own bearings and shaft, and the connection to the propulsion line is made with a conventional coupling. For this, we have made some mechanical design changes to the machines to accommodate the bearings. These two solutions are shown in the following picture.
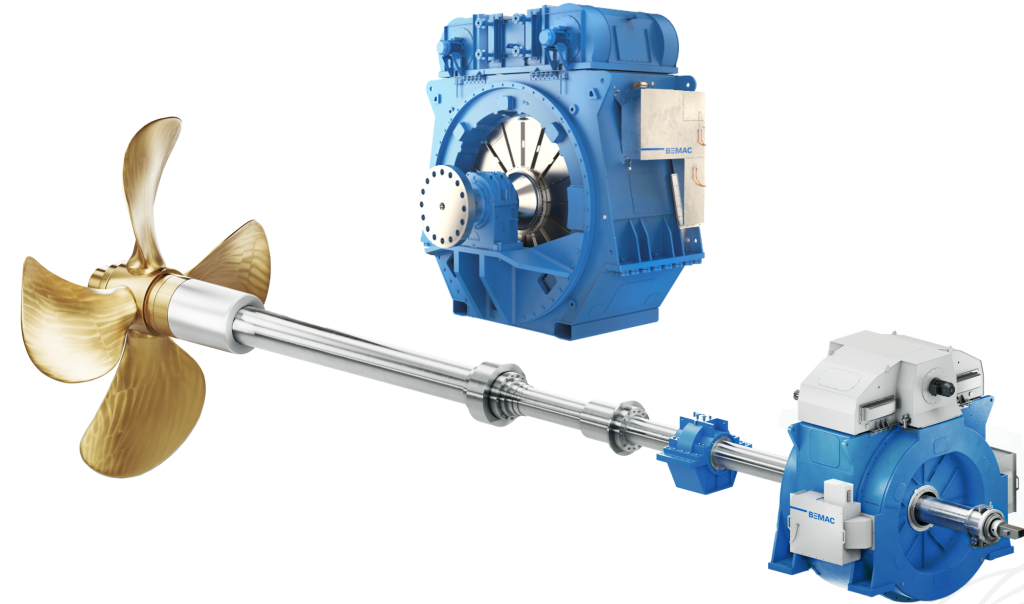
Tandem concept offers high redundancy
We have also developed a tandem concept, where two identical machines are connected on the same foundation. What makes this unique is that either of the two motors can be mechanically decoupled from the propulsion in case of motor failure.
In conventional solutions with PM motors, if the motor closest to the propeller fails, that motor must be removed from the propulsion line, and the second one moved into its position. So, from the redundancy point of view, this is as good as conventional electric motor types. The main drawback of PM machines is the fact that the magnetic field cannot be switched off in case of a machine short circuit. Therefore, they often need to be equipped with special protection concepts such as adding breakers at the star point.
But with this new tandem concept, redundancy is excellent. It can also be used in vessels having only one propeller. Currently, classification societies are hesitant to accept electric propulsion for single-screw vessels regardless of the electric motor type, unless there is some backup propulsion source, such as a retractable thruster that can move the vessel at sufficient speed in case of motor failure.
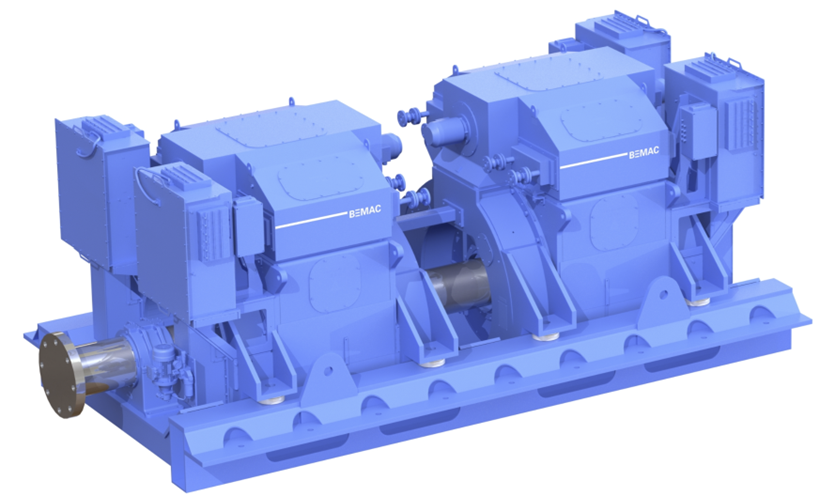
Learn more
Our existing field-proven marine machines are available from sub 1 MW up to 24 MW+, making it possible to sustainably propel very large ocean-going vessels. We have also unique full-power testing capabilities in our factories, ensuring that the machines and drives work as planned before they are dispatched to the shipyard.
You can read more about our propulsion motors here or come meet us at the Electric & Hybrid exhibition in Amsterdam in June.
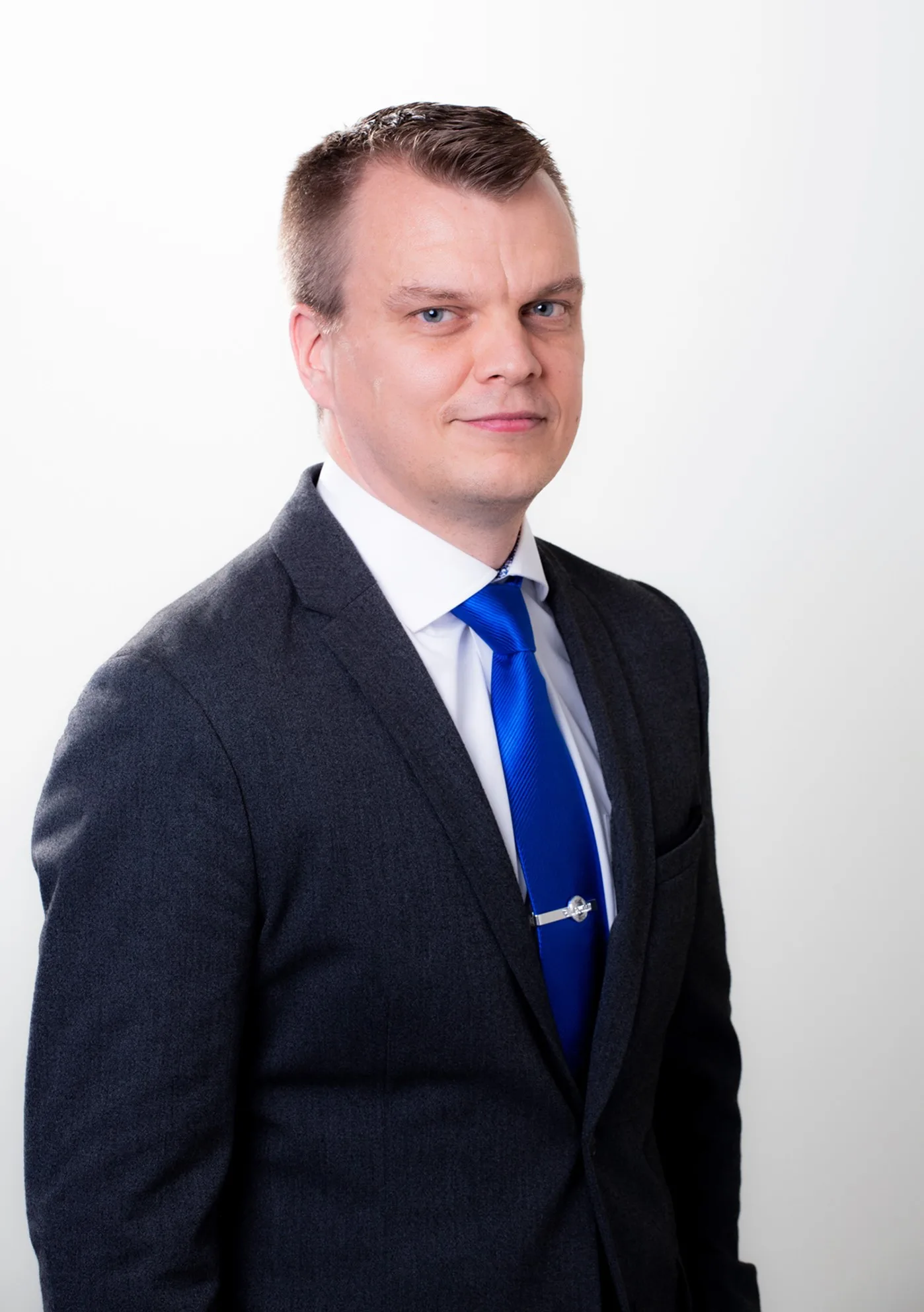
Product Line Director, Electric Machines
Jussi Puranen

Jussi has nearly 2 decades of experience in R&D and product development of electrical machines, and his main responsibilities are the product management and R&D of electric machines (especially PM machines). Puranen holds an M.Sc. (Technology) degree in Electrical Engineering and a D.Sc. (Technology) degree from the Lappeenranta University of Technology (LUT), Finland.