Did you know active magnetic bearing (AMB) systems are more energy efficient and have lower lifetime costs than tilting pad bearing systems?
We at The Switch regularly evaluate bearing systems when we supply high-speed electric machines. Our customers are looking for a bearing system that will provide the load capacity and stability their high-speed direct-drive compressor applications require.
Characteristics of two bearing systems
Tilting pad bearings have good load capacity and somewhat adjustable stiffness and damping characteristics. They can be engineered to suit rotor-dynamic requirements and make sub or super-critical operation possible across even a large speed range. And because oil-lubricated slide bearings, to which the tilting pad bearings belong, are widely used, there is already existing know-how about arranging condition monitoring and servicing for them.
Active magnetic bearings are still a more exotic bearing solution compared to “mechanical” bearings. While the active magnetic bearing does not need a lubrication system, its operation depends entirely on the controller to keep the rotor levitating. The controller forms a closed-loop system with the bearings and position sensors. Through the electromagnets of the bearings, it provides just the right amount of force to allow high-speed operation with minimal vibrations.
At the design stage, successful rotor-dynamic observability and controllability are paramount, as is the separation margin at critical speeds. Sometimes, at this point, technical features alone determine a clear winner. But when they don’t, how should a decision be made?
Cost might be the deciding factor
Another important consideration is the total cost of the bearings over the machine’s expected lifetime of 25 years.
Let’s assume the following application parameters as an example for discussion:
- The machine size is above 1.5 MW / 10,000 rpm
- The process requires an adjustable speed range, so a sub-critical design is favored
- The impeller at the shaft end is massive, requiring large bearing diameters for good rotor dynamics
- The impeller generates significant thrust load on the bearings
These requirements can be satisfied by either a tilting pad or an active magnetic bearing solution.
In a high-speed machine with a directly mounted compressor wheel, we know the bearing requirements, necessary auxiliary systems and the generated losses (there is always friction!) of both solutions.
Lowest initial investment with tilting pad bearings
We can use the following numbers to compare initial investment costs:
Investment | AMB | Tilting pad |
---|---|---|
Design | €80,000 | €8,000 |
Components | €72,000 | €27,000 |
Lubrication system | €0 | €15,000 |
Clearly, the initial costs of an AMB system are much higher. This is due to the required set-up costs in engineering, as well as the customized component manufacturing needed for each specific case.
Very low operating costs with AMBs
Now let’s look at the annual operating costs, where the primary factor is the price of electricity (assumed at EUR 0.12 per kWh):
Operation | AMB | Tilting pad |
---|---|---|
Electricity | €518 | €36,288 |
Oil, filter (*) | €0 | €1,200 |
Tilting pad bearings produce high electrical losses. Their high rotational speeds, large thrust load and bearing diameters contribute to bearing losses of over 30 kW, plus whatever the pump of the lubrication system requires. An AMB system manages losses of around only 0.5 kW.
Lifetime cost effectiveness of AMBs
So now, let’s look at how these yearly costs add up over the machine’s lifetime.
The chart below illustrates the yearly costs of the different bearing systems. Year 0 is the time of the initial investment, and the following years reflect the operational costs, assumed to remain the same over time (apart from service every 3rd year for tilting pad).
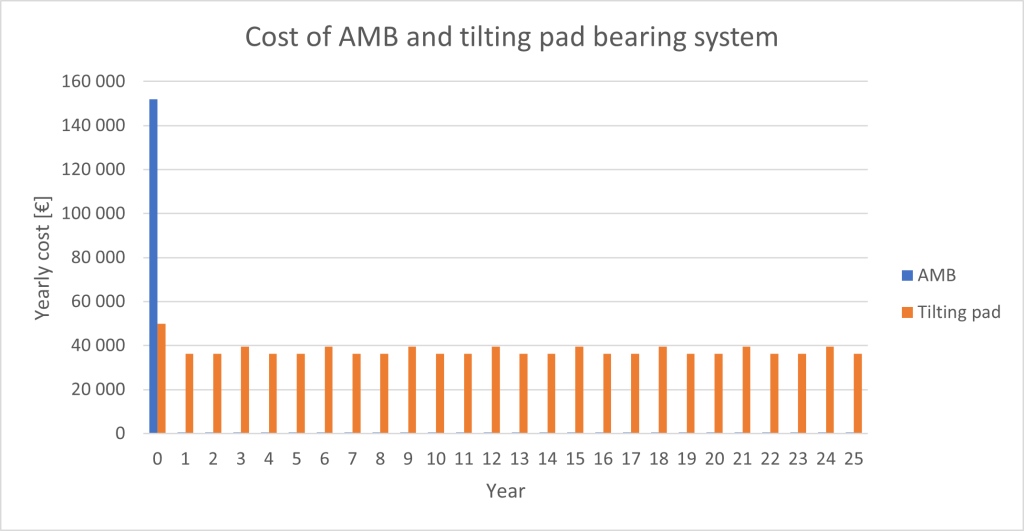
The final lifetime costs can be seen in the following table:
Lifetime cost | AMB | Tilting pad |
---|---|---|
€603,000 | €983,000 |
Justification over the lifetime is calculated by including the opportunity cost, which accounts for the difference in initial investments that could have earned value elsewhere. The opportunity cost is assumed here at 6%.
We can see that AMBs require a significantly higher initial investment. However, the lifetime costs of an oil-churning tilting pad solution for this high-speed application quickly exceed those of an AMB system, which, by comparison, has virtually no operating costs.
Even after accounting for the opportunity cost of the larger initial investment, the AMB solution is the better choice financially.
When cost is a deciding factor, choose AMBs
We shouldn’t be put off by the initial cost of AMBs. When all else is equal, AMBs can do the same job as tilting pad bearings and do it
- More economically
- With less maintenance
Over the lifetime of your direct-drive compressor, AMBs might save you more than a quarter million euros.
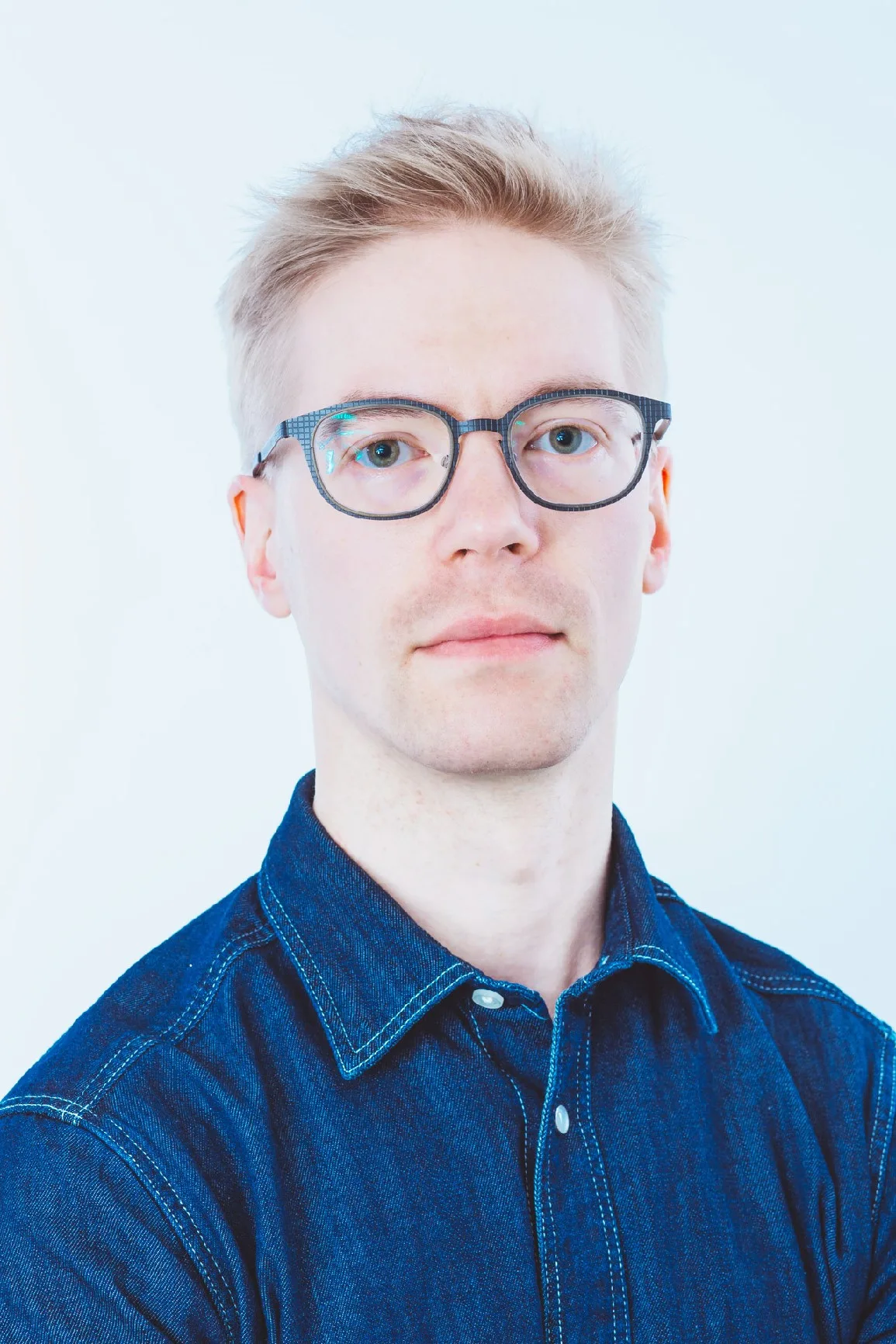
Product Manager, Solid Rotor Machines
Panu Hava

Panu Hava currently works as Product Manager, solid-rotor machines at The Switch. He has over a decade of experience in product development of electric machines, including industrial induction and synchronous machines as well as high-speed induction machines. Today, his main responsibilities are technical sales support for new tailored products and leading product development of high-speed electric machines. Hava holds a M.Sc. (Tech.) in Mechanical Engineering from Lappeenranta University of Technology.