IMO CO2 reduction targets are driving the marine industry toward a greener future. Green e-fuels are at the center of discussion, with the major challenges being the huge amount of energy needed for e-fuel production and the world’s constantly increasing energy consumption.
The marine industry is already working to reduce emissions by making vessel operations more efficient. Electrification is an obvious choice to increase efficiency and lower emissions. For instance, system integrators are already using The Switch’s portfolio of power electronics products and permanent magnet machines to create more efficient systems for a wide variety of vessels.
Battery is essential in electrification
Onboard batteries are an essential part of marine industry electrification today, and their energy capacity has increased very quickly. Only some years back, we were talking about 1 MWh installations, while now the biggest projects reach tens of megawatt hours and more.
And batteries need to be charged. Whether you charge them from shore, offshore or with gensets very much depends on the route and profile of the vessel.
Not enough shoreside infrastructure
But no matter which type of vessel we discuss – from fully electrified vessels to those that are only looking for a zero-emissions mode during harbor stays – there are not enough shore connections today to fulfill the coming needs of maritime electrification.
One challenge to building shoreside infrastructure is to ensure that enough energy is available where it is consumed. Grid capacity often creates a bottleneck. We will need more local microgrids to make charging power available right where it is required.
Whether microgrid expansion will support shore batteries or some other concept, only time will tell. But whatever shore connections are built, they must keep up with the increasing battery sizes on vessels.
Challenges in protecting shoreside charging systems
Shoreside charging infrastructure has many similarities to vessel grids. It can even be seen as an extension of them.
DC charging is a good example of this. It is an extension of the vessel’s DC distribution system. The DC connection between a vessel and the shore consists of cables, plugs, transformers, switchgear and other components, and these physical connections differ from harbor to harbor.
The lack of uniformity between harbors creates a big issue. How can we protect the DC electrical system when each harbor presents different conditions and requirements? How can we dimension it for many different environments while still ensuring selectivity? Without selectivity, a failure on one side of the vessel-shore connection could impact the other. This is the challenge with traditional protection devices, like fuses and breakers, where a failure in one part of the system takes down the entire system.
Ultrafast DC protection for any environment
Ultrafast protection is mandatory in every DC distribution system to ensure redundancy. The same principles apply to a DC charging link extending the system to the shore.
The good news is that this technology already exists.
As part of DC distribution, The Switch has developed a series of ultrafast protection devices based on semiconductor technology. The latest member of the family is the Electronic Current Limiter (ECL). The operating principle is simple: protection is based onmeasuring current levels. Any failures will activate protection within 10 microseconds (μs) once the current reaches a predetermined level.
The Switch protection devices have been in use on vessels for nearly two decades and are available to create safe and reliable shore charging systems.
Effective protection ensures operational continuity
These protection devices have much lower activation levels than those for fuses or breakers. And because of their fast response speed, these devices ensure continuity of operation in failure scenarios. The fault is detected and disconnected so quickly that the rest of the system keeps operating.
Importantly, system dimensioning can be standardized since factors like the environment, cables and lugs no longer play a crucial role. Instead, the current is measured, and the trip limit is set to a suitable level.
In addition, these protection devices are resettable. Resetting protection is simply a matter of switching the semiconductor off and back on. Having an ECL at both ends of the DC charging line ensures any system can operate safely and predictably in any harbor.
Welcome to easy and predictable protection in any environment!
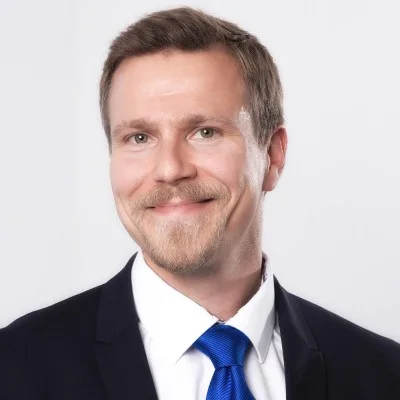
Product Line Director, Power Electronics
Teemu Heikkilä

Teemu has nearly two decades of experience in R&D and product development for high-power drives. He holds an M.Sc (technology) degree in Power Electronics from Helsinki University of Technology (currently Aalto University). His main responsibilities are R&D, engineering and product management for power electronics.