Superior efficiency, reliability and compactness are the core competitive advantages of permanent magnet (PM) machines. With our market-leading position and experience in delivering PM shaft generators, we believe these machines have a big role to play in the electrification of the deep-sea fleet. As shipowners look to lower emissions in line with IMO targets, PM machines offer a compelling solution.
In the context of propulsion, PM machines are used in electrical drive trains to generate the mechanical power that turns a propeller shaft or thruster. In contrast, PM shaft generators convert the rotational mechanical energy of the propulsion shaft – driven by the vessel’s main engine – back into electricity for use on board, reducing the need for diesel gensets.
In both of these applications, ‘permanent’ refers to the use of permanent magnets to create the magnetic field required for their operation. When electromagnets, which are used in conventional machines, require an external power source to generate a magnetic field, the magnets on the PM rotor generate a constant magnetic field with no need for an external power supply.
Magnetic fields interact
In a PM propulsion machine, two magnetic fields need to interact to produce the torque required to turn the rotor. This is achieved by feeding an external current into the stator winding inside the PM machine to create a rotating magnetic field. This field locks into the constant magnetic field of the rotor magnets, in effect, ‘dragging’ the rotor and making the rotor turn. The speed of the rotor – and hence the shaft line – can be precisely controlled by adjusting the frequency of the supplied current.
Operational benefits
Unlike traditional electric motors such as electrically excited synchronous machines (EESMs) and induction machines (IMs) that rely on electromagnets, PM machines generate their magnetic field without consuming additional power, eliminating rotor losses and enhancing efficiency.
- At the rated operation point, PM machines are typically around 2–4% more efficient than EESMs and 3–6% more efficient than IMs. The difference becomes even greater at partial loads, where these machines primarily operate. This increased efficiency can lead to millions of dollars in fuel cost savings and a reduction of several thousand tons of CO2 emissions over a vessel’s lifetime.
- PM machines are more compact. They occupy 30–40% less space in the engine room and are up to 50% lighter, making them ideal for vessels where space and weight are at a premium.
- PM machines also require less maintenance due to fewer wearing parts and components that could fail.
Cost benefit
Compared to diesel-mechanical propulsion, the initial capital cost of electric propulsion is usually a bit higher. In the long run, however, this solution can be significantly more cost effective due to fuel savings, depending on the vessel type, operating profile and electric system architecture. The greatest savings can be achieved in vessels which spend a significant part of their total operating time at reduced speeds. This is because some of the gensets can then be shutdown, while the remaining ones operate close to their optimal load point.
Additionally, using variable speed gensets and DC power distribution can further increase the efficiency without increasing the number of power conversion components. Fuel typically accounts for roughly 95% of lifetime costs, and this is where PM machines can make a big difference. For example, we have supplied more than 100 PM shaft generators for LNG carriers, with an estimated operating expenditure savings of USD 2 million per vessel over its lifetime.
- PM motors cost about the same as conventional electric motors, but their better efficiency helps reduce lifetime costs and contributes also to lower carbon taxes. This can be particularly significant for vessels that operate mostly at less than full speed. The lower maintenance requirement further reduces OPEX.
- The Switch’s PM machines are standalone, making them straightforward to assemble into a newbuild vessel. When it comes to retrofitting, there are no limitations from the PM machine perspective. However, the procedure for large vessels is complex as you need to drydock the ship and cut a hole in the side to install the machine, which can take several months.
Durability and reliability
PM machines are not a new invention and have been commonly used for the past two decades in megawatt (MW)-class applications, including large wind turbines and some azimuthing thrusters. Operating conditions are actually much harsher for wind turbines than the engine room of a vessel; just think about the North Sea in winter! In an engine room, it never freezes, there’s no salt in the air, and humidity is much less. This background ensures their durability and reliability in maritime applications.
- Beyond CO2 emissions, PM machines are comparatively quiet and produce minimal vibrations compared to conventional systems, thereby reducing noise pollution and its impact on marine life. In one fishing vessel case, our PM system received the DNV silent notation, which puts strict limits on underwater radiated noise (URN), highlighting its minimal noise levels.
- All MW-class PM machines use magnets made of a mixture of neodymium, iron and boron. With powerful magnetic flux, they are designed to last the entire 20- to 30-year lifetime of a vessel. This longevity, which is based on actual measurements, dispels a common market misunderstanding about the need for magnet replacement.
Redundancy and safety
Class requirements for PM machines were formalized over the last decade, and the solution is now standard. However, if the vessel has only one shaft line, then electric propulsion is not fully accepted by classification societies, regardless of the electric motor type. To overcome this issue, we have developed a tandem concept comprising two motors connected on a common shaft. Should one machine fail, the second machine can continue operation, providing at least 50% of the full power. Due to the cubical power-speed dependence of the propeller, this is sufficient to move the vessel at around 80% of full speed.
- Because the magnetic field in PM machines cannot be switched off, another class requirement is having a decoupling mechanism inside the machine to lock the rotor in place when the motor is not in operation. This is necessary because the PM machine’s constant magnetic field can induce voltage even when the motor is off – if the rotor continues to rotate. The decoupling mechanism holds the rotor secure and prevents fault currents and unwanted voltage induction at the machine terminals.
- Often, we also use a star-point circuit breaker in PM machines to prevent fault currents and manage risks associated with the magnetic field, especially in shaft generator applications. It ensures that maintenance can be performed safely and helps protect the machine and crew from potential electrical hazards.
Market trend
PM motors are now very common in smaller vessels such as ferries but also in MW-class propulsion systems used by many vessel types. For instance, The Switch has supplied 3 MW PM propulsion motors for the CSL bulk carrier M/S Nukumi, which won “Vessel of the Year” at the 2023 Marine Propulsion Decarbonisation Awards.
The major challenge is that larger deep-sea vessels are still using diesel-mechanical systems, but there is a shift afoot due to tightening regulations. The IMO’s target of significantly reducing greenhouse gas emissions is forcing shipowners to adopt cleaner technologies, and PM propulsion is one of the most effective solutions.
- We were the first in the market to supply PM shaft generators, which took a lot of convincing. Then, it was mostly about fuel savings, but now it’s more about emissions reduction.
- We don’t see any issues with market acceptance. Since 2015, we have sold more than 400 PM shaft generators for large ships. Together, they have several millions of cumulative running hours, so the basic technology is proven. Our power electronics products also make it very straightforward to connect various kinds of energy sources into the vessel’s power system, such as batteries, fuel cells and wind/solar, which will also be more common in the future.
Modular design
Our focus at The Switch is on direct-drive systems with no gearbox (meaning fewer components), which we believe is the most reliable solution for MW-class propulsion applications. Our biggest differentiator is our flexibility in offering tailor-made designs optimized for customer requirements. We precisely match PM machine capacity to the vessel’s operational speed and power without over-dimensioning. Our modular design approach minimizes engineering costs from project to project. We can adapt interfaces and move things around, for example, adjust the cooling system or modify the shaft diameter.
In conclusion, PM machines offer a versatile solution for future electrical propulsion needs as the industry adopts more sustainable solutions. Certainly, their efficiency, compactness and reliability make them a superior choice versus conventional EESMs and IMs. We’ve definitely entered the PM machine era, and the rapid growth rate of inquiries we are receiving, particularly for propulsion applications, serves as clear evidence.
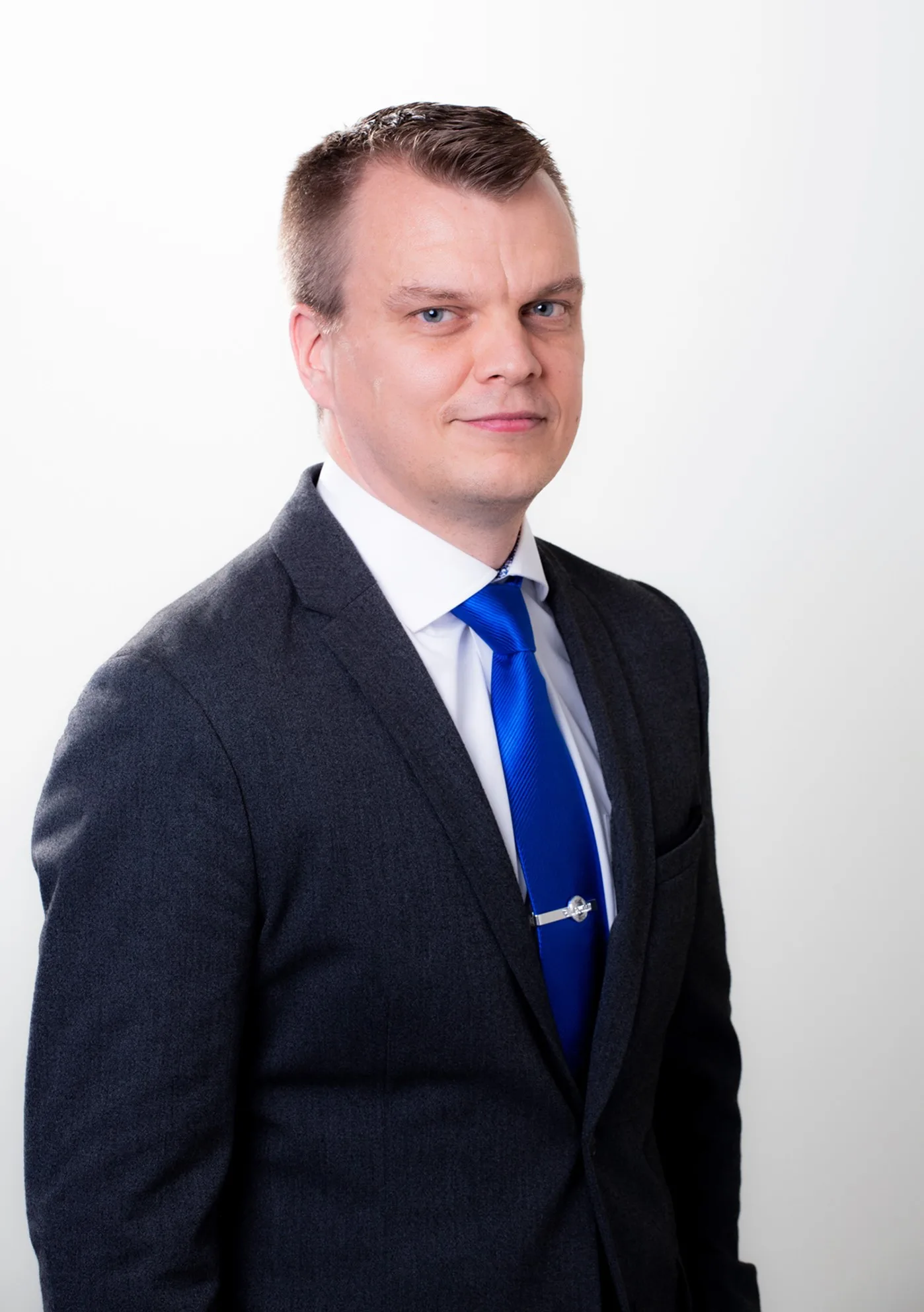
Product Line Director, Electric Machines
Jussi Puranen

Jussi has nearly 2 decades of experience in R&D and product development of electrical machines, and his main responsibilities are the product management and R&D of electric machines (especially PM machines). Puranen holds an M.Sc. (Technology) degree in Electrical Engineering and a D.Sc. (Technology) degree from the Lappeenranta University of Technology (LUT), Finland.