The cooling system for a vessel’s electrical machines and drives is of paramount importance. Inadequately handled thermal stresses can cause an electrical system to age prematurely or even fail. A successful cooling system design must completely address all potential issues.
Air-cooled systems are the cheapest and easiest to maintain. However, liquid-cooled systems come with so many advantages that they must be seriously considered. For further discussion of these advantages, see our previous blog.
We have years of experience with cooling systems for wind and marine power converters used in standard drives and are well acquainted with their numerous benefits – as well as their weaknesses.
For marine systems, we have developed an innovative design that incorporates the best aspects of liquid cooling systems while correcting the shortcomings of standard solutions.
Characteristics of standard liquid cooling designs
Standard systems cool each drive with a dedicated cooling station with its own isolated water loop. Each cooling station is dimensioned for peak load, and redundancy is handled by a backup cooling system for each.
However, each internal cooling loop is sensitive to unfiltered impurities, which can become more concentrated over time, and algae can grow in the channels. This – together with the use of heavy turbulators and the higher pressure drop over the drive inherent in a liquid cooling system – makes the channels vulnerable to blockages.
Heat exchangers are used in many liquid cooling systems but are not ideal for most marine and offshore applications because of their size and complexity.
Heat exchanger systems require more space for their instrumentation and components, including temperature, flow and pressure monitoring, ventilation and control systems as well as the need for technical or seawater on the primary side. A heat exchanger also adds an extra thermal barrier. As a result, temperature control is slower and less responsive because changes must propagate through the heat exchanger before affecting the drive. Thermal losses are also somewhat higher, which can limit peak performance under high loads. Additionally, more components can fail and need maintenance and spare parts.
Innovative design resolves system vulnerabilities
Instead of individual cooling stations for each drive, we use the already existing low-temperature (LT) freshwater cooling system that is a much larger, shared and centralized. It is also integrated with other onboard water systems, accessing water from the same sources. This much larger volume of water circulates in a much larger loop, passing through each individual drive and other equipment connected to the same system.
We also use slightly larger pumps and lighter turbulators in the freshwater cooling circuit to increase the pressure and circulation speed of the system. Faster circulation ensures that impurities move faster throughout and do not cause blockages. The higher circulation speed also ensures no air is trapped in the system. And the turbulators allow for better cooling performance.
The internal piping in the drives must handle “red metals” like copper, so it is made of copper, stainless steel, PEX and brass, although the feeder pipes can be black steel. With only one central cooling station, however, overall piping costs are less than for standard systems.
Most importantly, our cooling systems do not use a main heat exchanger. We believe the resulting space savings, energy efficiencies and system responsiveness are more essential.
And without the main heat exchanger, the coolant is much closer to the heat-generating components. Efficient heat removal leads to better handling of high-power loads with reduced thermal losses, improved overall energy performance and lower temperature for the electrical components, which again means longer lifetime.
No main heat exchanger, along with fewer pumps and monitoring instruments due to the shared system, means many fewer components overall, reducing the possibility of failures. All this brings greater robustness – the key to reliable and long-lasting marine drives.
Specific benefits of our new design
Some of the resulting benefits include:
- Larger volume of water diluting any impurities that might otherwise damage the electrical system
- No secondary cooling system backup needed specifically for the drives, as redundancy is already provided by the primaryonboard cooling system
- Fewer components, resulting in lower costs, fewer failure points and reduced maintenance
- Smaller size and more compact footprint
- The centralized cooling unit dimensioned for real load, not just for peak loads
- Self-ventilating system with no need for “bleeding”
- Reduced thermal losses for greater overall energy performance
- Better reliability
Today, our innovative design cools more than 1,500 marine drives in vessels operating around the world.
Please get in touch if you have further questions. We’re always interested in discussing creative solutions to today’s marine industry problems.
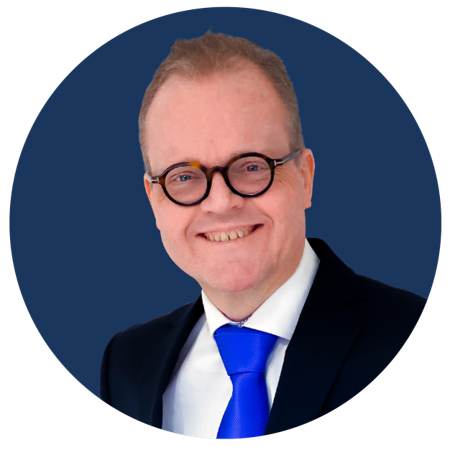
Chief Expert, Marine Concepts
Asbjørn Halsebakke

Asbjørn Halsebakke is leading his team in engineering marine drive solutions, frequency converters and rotating machinery, which are in use today with the utmost reliability on vessels throughout the world. Before joining The Switch, Halsebakke worked for Aker Kværner Elektro AS in Norway to develop frequency drives and perform sea trials and commissioning. Halsebakke graduated from Narvik University College with a Master of Science in Electrical Engineering. He also attended the University of Bergen, where he studied elementary physics and mathematics.